Laundry Room Effectiveness: What You Need to Keep in Mind Now
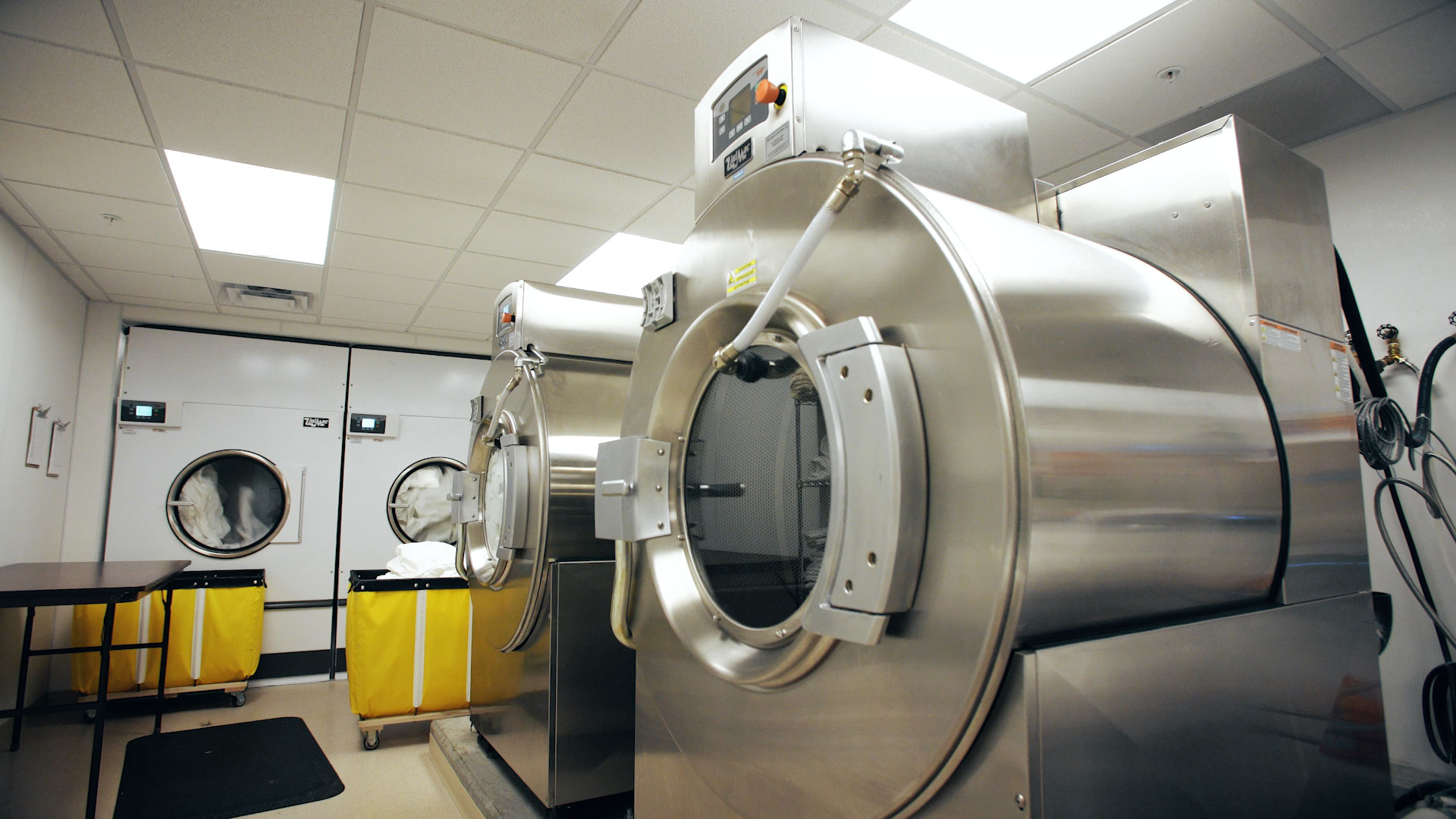
Our world has changed seemingly overnight. In the on-premises laundry world, especially laundries serving long-term care and medical facilities, the demands have been great. Pressure to make increased daily throughput numbers is ratcheted up with an emphasis on the greatest degree of safety precautions. Facility lockdowns make it even more difficult in the event equipment requires service.
It’s important to look at the current state as less of an anomaly and more as an indicator of how we’ll likely need to operate in the future. Equipment sizes, features and technology that perhaps weren’t considerations before, may now be must-haves for your operation moving forward in a post-COVID-19 world.
While you might not be immediately pondering a laundry room upgrade, create a log of any current pain points. Your insights documented now will be immensely helpful as you begin looking to retool in the future. Below are a few conversation starters that may drive your needs list.
- High G-Force – If greater throughput demands have created a bottleneck on the drying side, you may require a high G-Force (350 + G-Force) washer-extractor. High G-Force greatly reduces drying times by removing significantly more water from loads vs. low G-Forces of 85 to 200. This is also the most efficient way of removing moisture from loads.
- Moisture sensing – Moisture sensing is another feature on the dry side to consider. With CDC guidelines recommending high heat and laundry be dried completely, moisture sensing technology takes away the guesswork of employees wasting time checking loads (and wasting utilities by doing so). Moisture sensing technology dries loads to a pre-programmed moisture content and stops the tumbler. This feature also eliminates costly over-drying of loads, which wastes utilities and degrades linens faster (all that lint in the lint drawer is coming from somewhere – your linens).
- Laundry management – Laundry management systems are perhaps one of the most important new technologies in today’s crisis. Offering remote access to a wealth of data, including documenting cycles used (ensuring process control), highest temperature reached in each cycle (CDC recommendations are 140-160 degrees Fahrenheit to kill bacteria) and more. They can act as the eyes and ears of the laundry when a manager isn’t on-site, offering real-time views of what is happening. With so much riding on infection control, laundry management systems are essentially the insurance policy verifying no corners are cut and no issues are on the horizon.
- Carts and other ancillary equipment – Do you need more laundry carts or an upgraded design that’s easier to keep sanitized? Are your current carts color coded or clearly marked as to what ones are for soiled linens and those used only for clean linens? Are your folding areas and tables able to be easily sanitized? Do you have enough spray bottles and rags for wiping areas down as frequently as necessary during this crisis? Do you have enough bags on-hand and in the right areas on the floor for bagging contaminated linens?
- Service – You may be looking at the service and support capabilities of your equipment distributor. With many facilities locked down during the crisis, working with a distributor that has video troubleshooting may be a prerequisite driving future purchase decisions. In addition, overall service hours and parts availability are equally important. The crisis may have exposed your current distributor’s deficiencies in these areas, or they may have strengthened their standing with your facility by going above and beyond. You also may be identifying the need to have a greater variety of replacement parts on-hand to perform lighter service work in-house.
- Greater capacity? – Has the need for greater throughput uncovered a lack of capacity in your operation? While larger machine capacity may be a target, managers should also consider how soiled linens flow into the laundry. Often multiple smaller capacity machines may make the most sense, because not all linen arrives at once – waiting around for a full load for a large capacity machine can waste valuable time. Use this time to note how loads are flowing through your laundry.
- Finishing equipment – Are flatwork finishers a way to not only increase quality but also throughput? When combined with high G-Force washer-extractors, often linens emerge from the washer ready for finishing or in need of minimal conditioning in the tumble dryer.
- High pressure spray rinse options – Washer-extractors utilizing a high-pressure spray rinse are quite effective at removing residual chemistry versus conventional bath rinses – a huge advantage in the long-term care environment, where pressure ulcers are exacerbated by leftover chemicals in linens. Because of this, spray rinses can also be deployed in crisis like the one we are in as a pre-rinse step with the drain valve open as a way to remove soil before starting the wash cycle. With the drain open, soil is removed from the wash cylinder immediately.
- Chemicals – Are your current chemicals and chemical supplier serving you well? Has the crisis uncovered any necessary changes to your laundry chemical needs or doses? Is your chemical representative coming to you with new ideas to obtain the best results and quality? Are they able to also supply wipe-down supplies for cleaning controls, handles, folding tables, etc.?
There’s no doubt these are tough times…and we are all trying our best to make it through the day and get everything done on-time. However, there’s also an opportunity to look at our laundry operation with new eyes. Tough times definitely uncover process breakdowns as well as equipment shortcomings. Take note of these revelations and let them guide your purchasing and other decisions now and in days ahead. Doing so will ensure your operation is streamlined and better positioned to manage through a future crisis.
Find your local expert here.