What to Do When Your Commercial Laundry Equipment Breaks Down
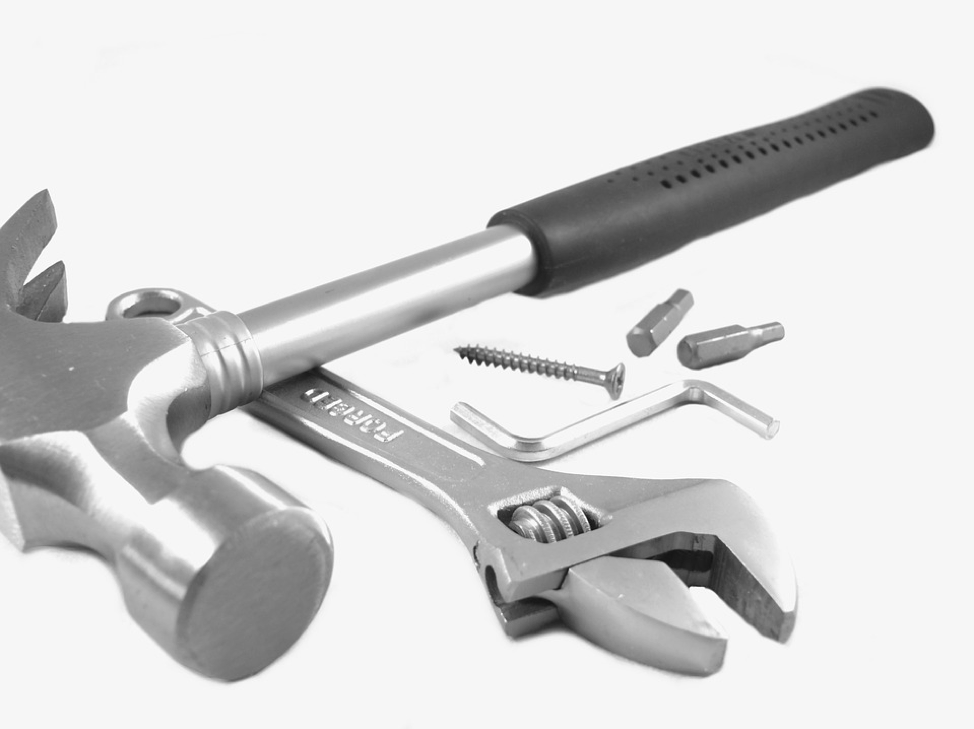
With proper installation and a routine maintenance schedule, your commercial laundry equipment should be relatively problem-free. However, nothing is perfect. You may run into a broken down machine or maintenance issue here or there. Unfortunately, for those of us in the laundry industry, that can have a serious impact on productivity and efficiency in our on-premises laundry operation. Nobody wants that. Check out the following tips to tackle maintenance issues like a pro and get machines back up and running quickly.
Don’t panic.
It’s easy to get frustrated or go into panic mode when something happens with your laundry equipment. You don’t want to tackle a problem when you’re upset or anxious — it generally makes the problem worse. Tacke any immediate safety issues (see the next step), then do what you need to do to calm down and approach the issue with fresh eyes.
Secure the area.
Always put safety first. If there’s water leaking or a potential electrical hazard, you’ll want to be sure you tackle that right away. Depending on the situation, that could mean shutting off the water valve, unplugging the machine, putting up wet floor or out of order signs, or keeping employees out of the area.
Consult your manual or equipment guide.
Once the area is secured, this is your go-to next step. These handy guides are full of important maintenance information, guidelines, and safety information. You may find the answer to your problem right at your fingertips.
Contact an expert.
If you’re not 100 percent sure what the problem is and how to fix it, don’t attempt it. The last thing you want is to damage your machine. Always contact a certified laundry equipment expert. They have the experience, knowledge, and tools to get the machine back up and running as soon as possible. Keep in mind, not everyone on the internet is an expert either, so be wary of chat rooms and open forums. It’s best to contact a professional directly.
Got a maintenance issue? Contact our team of on-premises laundry experts
Document it.
You’ll want to document any and all maintenance along the way. Notes, images, and documentation will help the service technician repairing your machine offer advice and/or diagnose the problem. A good record may also be necessary if you have to file a claim with insurance or end up selling the machine at any point. UniLinc, our OPL control system, allows you to instantly access your laundry equipment service history logs, receive error notifications, and view performance reports. The best part is you can do it remotely with wireless networking, so the information is accessible anywhere!
Check out our handy maintenance tips